What is sheet metal fabrication?
Talking about sheet metal fabrication, the first word that can help you get an idea of it is paper-craft. Cutting, folding, and gluing the pieces of paper to form a new shape.
Sheet metal fabrication is a process that initially turns the metal into thin and flat sheets. Then the sheet metal was made into various desired shapes using different manufacturing techniques. This article categorizes these techniques into cutting, forming, assembly, and surface treatment.
The common metals used for sheet metal fabrication are copper, aluminum, stainless steel, zinc, etc., The term used for the thickness of sheet metal is gauge; the range varies from 3 gauge (0.2391 in.) to 36 (0.0067in.) gauge. The greater the gauge number, the thinner the steel metal.
Sheet metal fabrication has wide applications in consumer goods, automotive, HVAC(Heating, Ventilation, and Air Conditioning), and aerospace.
Forming
In essence, forming in sheet metal fabrication is folding the paper pieces into desired shapes in making paper-craft, but sheet metal fabrication uses more advanced and complex techniques.
Forming in sheet metal fabrication is a process that deforms the sheet metal into desired shapes without cutting it. The main forming processes are bending, stamping, and spinning.
Sheet metal bending utilizes a press brake, the term used for the sheet metal fabrication industry, as a bender to bend the sheet metal into useful shapes. U shape and V shape bending are the standard bendings. The bending angle usually varies from 0-120 degrees, depending on the customer’s request. Now, we have more advanced technology for the bending process, we can input the data to the robotic arm, and it operates automatically.
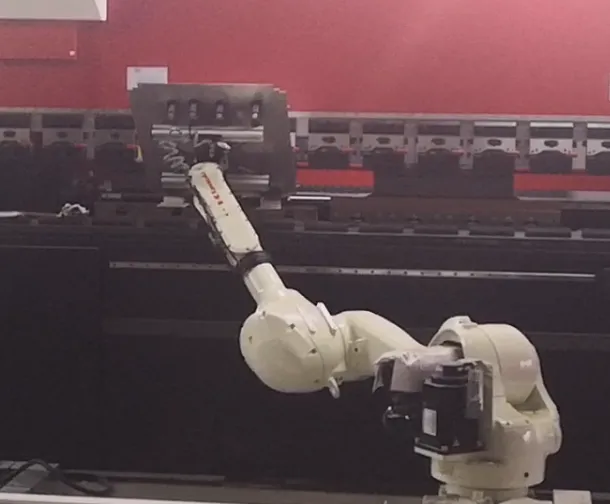
working robotic arm
Stamping is also known as pressing. This method uses tremendous force to push the sheet metal on a die surface. The sheet metal is deformed and forms a new shape.
Spinning is a less common forming method in the sheet metal fabrication industry. It turns a circular piece of sheet metal into a cylindrical or axial rounded shape. A lateral force performs this by a spinning machine at high speed placed against the surface of the circular sheet metal. The roller of the spinning machine supports the rounded sheet metal and gives it the final shape. Spinning is mainly to create round shapes like cylinders and cones.
Assembly
This is the final process in sheet metal fabrication unless it does not require surface treatment, which joints the produced pieces in previous operations. The two commonly used techniques for assembly are pressing rivet fasteners and welding.
Pressing rivet:
Just as its name implies, this is the process of pressing the rivet with a downward force into the thin sheet metal. This allows for the formation of riveting nuts, then using bolts to fasten the sheet metal pieces by joining the nuts and bolts.
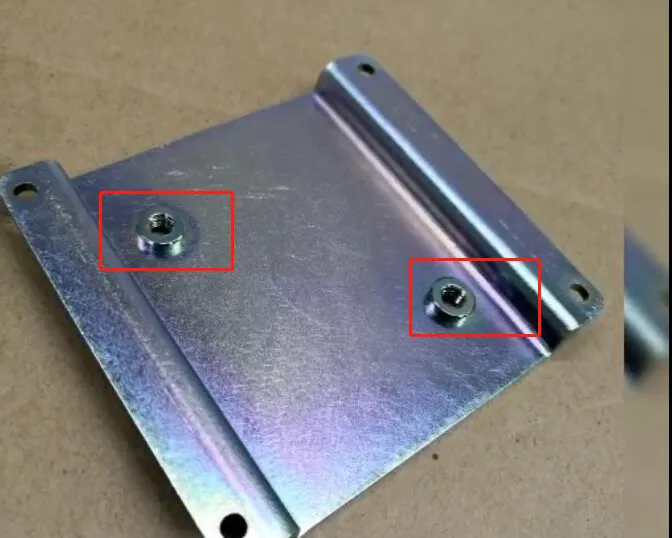
pressed rivet
Welding:
The welding process is one of the most commonly used techniques to assemble sheet metal products. Once the metal pieces are formed, the pieces can be joined together with welding. Thus, the metals are fused to form a solid connection. In essence, welding is a process that melts sheet metals. Welding of common sheet metals for stainless steel and aluminum is particularly doable. Welding methods would vary depending on the types of metals. MIG(Metal Inert Gas) welding and TIG(Tungsten Inert Gas) welding are two example welding methods.
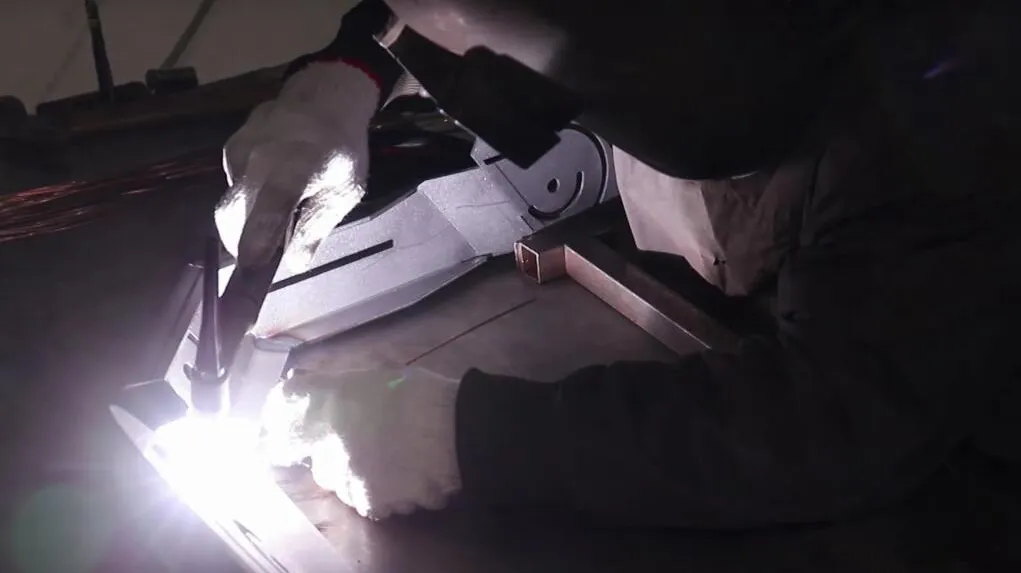
welding operation
Surface treatment
This is the ultimate process in sheet metal fabrication. After all the metal pieces are cut, formed, and assembled depending on the custom’s requirements, choosing different methods to finalize the well-produced metal parts. Anodizing, powder coating and electroplating are the three commonly used techniques for surface treatment. The surface treatment enhances the corrosion resistance and can change the texture and colors of the metal.
Anodizing is a surface treatment method for aluminum sheet metals. The basic principle of it is forming a layer of Al2O3 on the surface of the metal by anodized oxidation. This layer enhances the resistance of corrosion and the hardness of the metal. However, anodizing is only doable for aluminum sheet metals. Anodizing is widely used in making precision instruments, aerospace piece, automotive parts, and etc.
Powder coating is a process that uses dry powders to make a protective cover or coat on the surface of sheet metals. Compared with anodizing, it is helpful for more different metal types like stainless steel, steel, and aluminum.
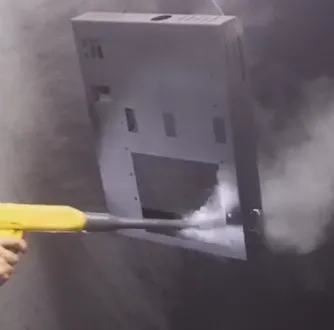
on going powder coating
Electroplating is forming a coat or cover by using electrodeposition, converting the cathodes to anodes. This process enables the sheet metal to become more smooth and more good-looking.
Types of sheet metal:
Steel is relatively cheap and usually used in making furniture, cabinets, and larger structures like the gate of garages.
Stainless steel has good corrosion resistance, commonly used for kitchen accessories, laboratory instruments, and HVAC pipes.
Aluminum is less common because it is more expensive than other metals. Still, it has strong corrosion resistance and is lighter and more robust—consumer products like smartphones, computers, and automotive parts.
Conclusion
Bingo! After these four main processes, an initially flat sheet metal turns into a workable part. Cutting, forming, assembly, and finalizing it with surface treatment. Sheet metal fabrication is flexible and versatile. Various industries have the demand for sheet metal. For example, aluminum sheet metal is heavily used in the automotive industry and aerospace due to its characteristics of aluminum. Sheet metal fabrication is crucial to utilize aluminum in a specific shape. Sheet metal fabrication is also significantly important for the HVAC industry. Metals are needed to create the tubes for transferring heat, fresh air, and humidity. Knowing the processes and techniques (cutting, forming, assembly, and surface treatment) is necessary. Understanding these processes gives you a clear idea of choosing your custom design of a part.